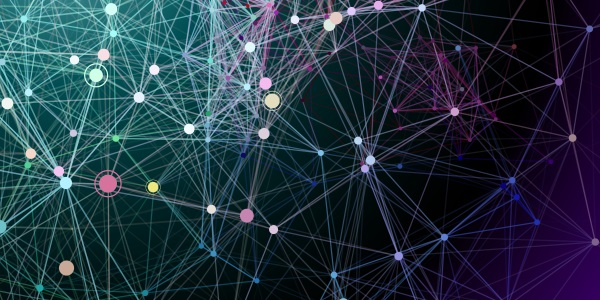
When choosing a fire alarm system for your building or business you can be faced with a number of different choices. Arguably, one of the most important decisions facing owners is whether to opt for an open or closed protocol system.
What’s the Difference?
Fire alarm systems include a variety of different components, all of which communicate with each other. The language that these devices use to communicate is called a ‘protocol’ – and this is what can be ‘open’ or ‘closed’.
Companies who provide open protocol systems disclose the relevant technical data required for manufacturers to produce compatible devices. These companies can work with any number of different manufacturers, providing customers with a range of different suppliers to choose from.
Companies who produce closed protocol systems don’t disclose their technical information, and therefore customers are forced to acquire all of the relevant components from a single source.
Open Protocols
Open protocol fire safety systems offer customers a greater degree of flexibility, and this is one of their main benefits. As a result, customers can choose from a variety of different suppliers, allowing them to install components which are completely suited to their specific circumstances.
Other factors such as repairs and upgrades can be completed by virtually any trained engineer, which allows customers to take advantage of an open market and choose a technician who offers the most value for money or expertise. Another advantage to open protocol is that the co-operation between different companies almost guarantees that a component is well tested and reliable.
There are very few disadvantages to utilising an open protocol fire alarm system but they should be kept in mind prior to making a final decision. As this system allows users to install components from different manufactures there is a slight chance that some of these devices won’t be compatible after a full system upgrade.
Customers can choose from a wide range of engineers when they wish to have their system upgraded or repaired, but this is the basis of another disadvantage. With so much choice available, there is a chance that an untrained or unprofessional engineer will work on the system, which can obviously be risky.
Closed Protocols
Whereas open protocol systems allow customers a greater degree of choice, closed protocol systems are much more insular. Customers can only install components from the same company who have provided the overall system due to compatibility issues.
Furthermore, clients can only use engineers from that company when repairing or upgrading their equipment.
Manufacturers claim that one of the main benefits of utilising a closed protocol system is harmony, as all of the components have been manufactured by the same company they are designed to work together successfully. Another benefit to utilising this system is that customers can often receive a discount on their initial quote.
In terms of criticisms, closed systems have their fair share. Customers are forced to use the same company when they require spare parts or repairs. And with no competitors forcing prices down, these services tend to be expensive, and parts can even become discontinued if the manufacturer decides to do so.
Furthermore, customers are unable to choose from a wide range of equipment and therefore they may not be using the most suitable components for their circumstances.
Lastly, within closed systems upgrades are made when and if the manufacturer chooses to make them, which isn’t ideal for the customer.
Choosing the correct fire detection protocol system is dependent upon circumstance. Open protocols offer a greater degree of freedom, choice and long term value for money; however if cost is not a primary concern you may prefer the closed protocol system which can offer a straightforward alternative.