Risk assessments play a vital role in keeping your workplace safe and are an essential pillar of an effective health and safety strategy, whichever industry you are in. Identifying and managing your workplace risks regularly enables you to protect your employees by mitigating the hazards and supplying the necessary training, whilst also ensuring you remain compliant. However, many risk assessments fall short due to missing or skimming past some of the most crucial elements.
So, to help you strengthen your processes, here are five essential components every workplace risk assessment should include.
1. Clear Identification of Hazards
The first step of any risk assessment is to thoroughly identify all the potential hazards across the workplace. This includes all physical, ergonomic, or long-term hazards, many which may not be immediately obvious. This creates a clear outlay of the risks, so that you can work towards a plan to mitigate them effectively.
During your assessments, you should also consider the impact of any changes occurring throughout your workday, including any lighting, weather, personnel or processes that may differ. Reviewing your incident reports regularly can also help reveal common health and safety risks and failings.
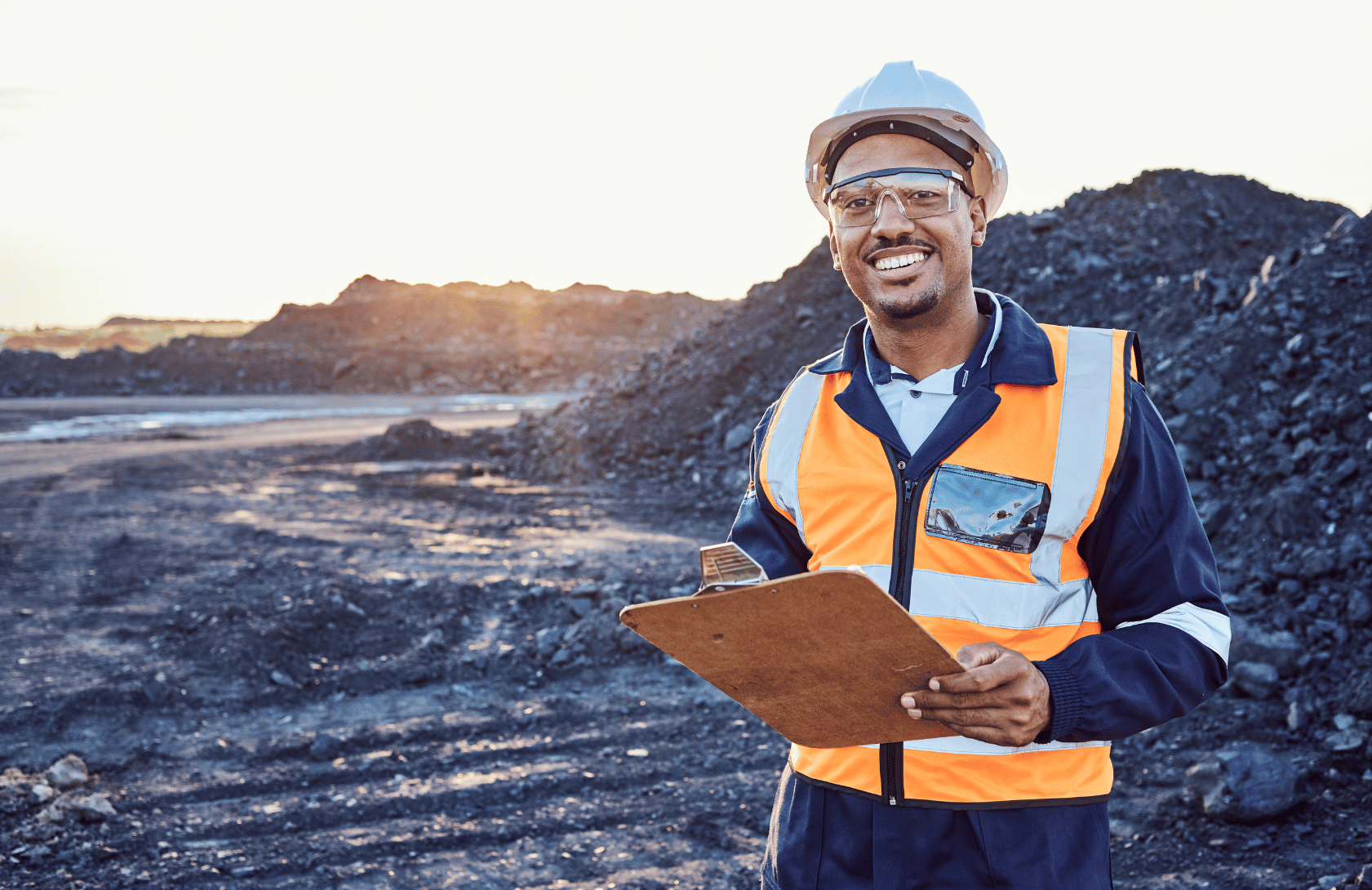
2. Who is at risk?
When working towards achieving safer workplace practices, understanding who might be affected by each hazard is crucial in order to pinpoint how to best protect the individuals. This includes not only employees but also contractors, visitors, and even members of the public – depending on your workplace layout and operations.
This allows you to adjust the processes according to their level of experience and knowledge via a range of techniques, whether that be improving your staff training, moving staff around, or even changing the processes entirely. This also opens up the opportunity to spot developing patterns, thereby potentially preventing any individuals from being overexposed to hazards.
3. Implementing Control Measures
With the vulnerabilities now identified, you must evaluate the level of risk each hazard presents and identify all existing control measures. Commonly this can be done through a rating system such as a risk matrix/register, to easily prioritise the most dangerous areas. Determine if the control measures are adequate or if further action is required to bolster your health and safety practices to reduce the risks.
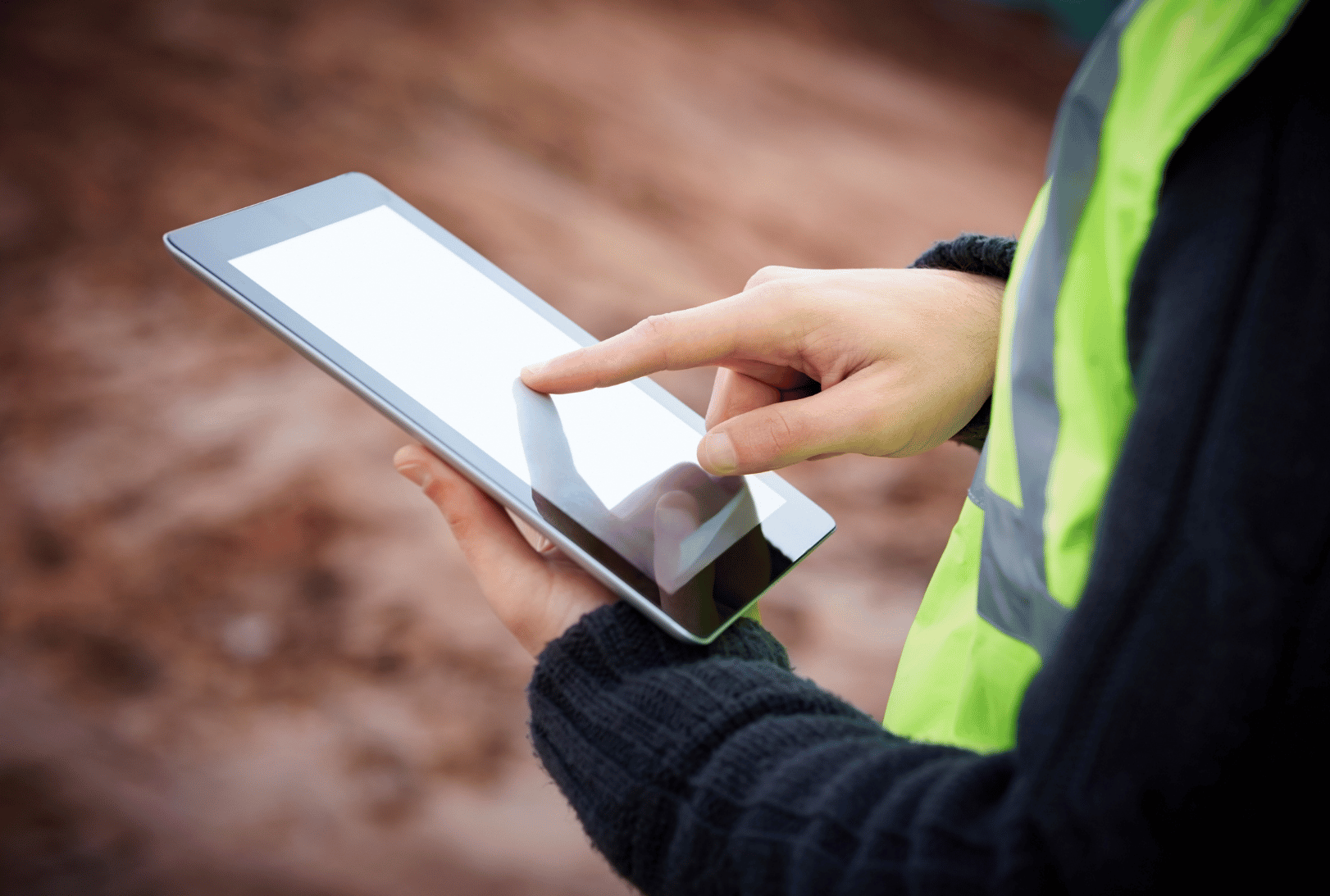
In this step, it is also crucial to consider how hazards may overlap and interact with each other, as often long-term risks and fatigue can increase the chances of a health and safety failing.
When implementing mitigation techniques, it is important to remember the hierarchy of controls, providing a guide to the most effective strategies:
- Elimination – Removing the hazard completely
- Substitution – Replacing the process or hazard with a safer alternative
- Engineering Controls – Changing the systems to minimise risk exposure
- Administrative Controls – Changing practices to reduce the potential risk
- PPE – Directly protecting the individual from the risk
4. Employee Involvement and Consultation
No one knows your workplace quite like your staff, as interacting with different parts of their working environment day in day out gives them a unique perspective and understanding of potential health and safety issues and concerns. Co-operating with your employees during a risk assessment is crucial to revealing the overall picture, helping you be aware of hazards that may have otherwise gone unnoticed whilst also enhancing your health and safety culture – making staff feel heard and valued.
During this step, it is also vital that you ensure all staff are up to date with the latest emergency plans and processes to verify their safety and others in the event of an emergency.
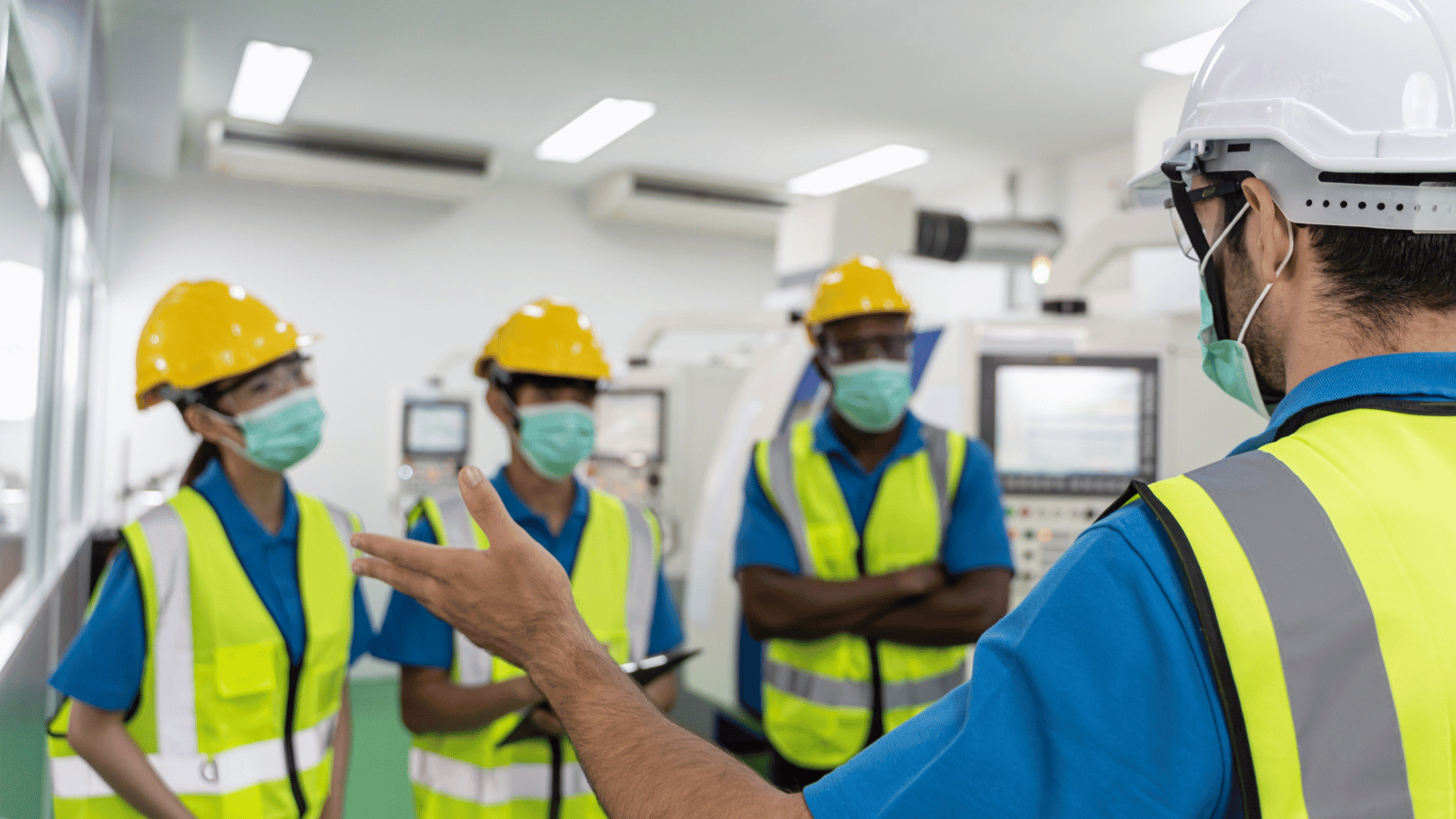
5. Introducing a Review Schedule and Documenting
Finally, workplace risk assessments are not one-off exercises. They should be living documents, updated and reviewed whenever there are changes in procedures, equipment or personnel, with significant changes demanding a full re-assessment. With this in mind, scheduled review intervals are essential to upkeep a safe workplace. Depending on your working environment and the risks involved these timescales can fluctuate, being unique to your organisation, generally sitting between every quarter to biannual reviews
On top of a regular review cycle, make sure you are thoroughly documenting your finding. This is not only good practice, but it’s a legal requirement across the UK. A clear and structured record shows that the risk assessment was completed properly and outlines who is responsible for actions and their deadlines.
Documenting and scheduling reviews is often made easier through the use of standardised templates, helping your reviews to meet the same criteria. This can be further aided by risk assessment software to maintain consistency and keep within deadlines.
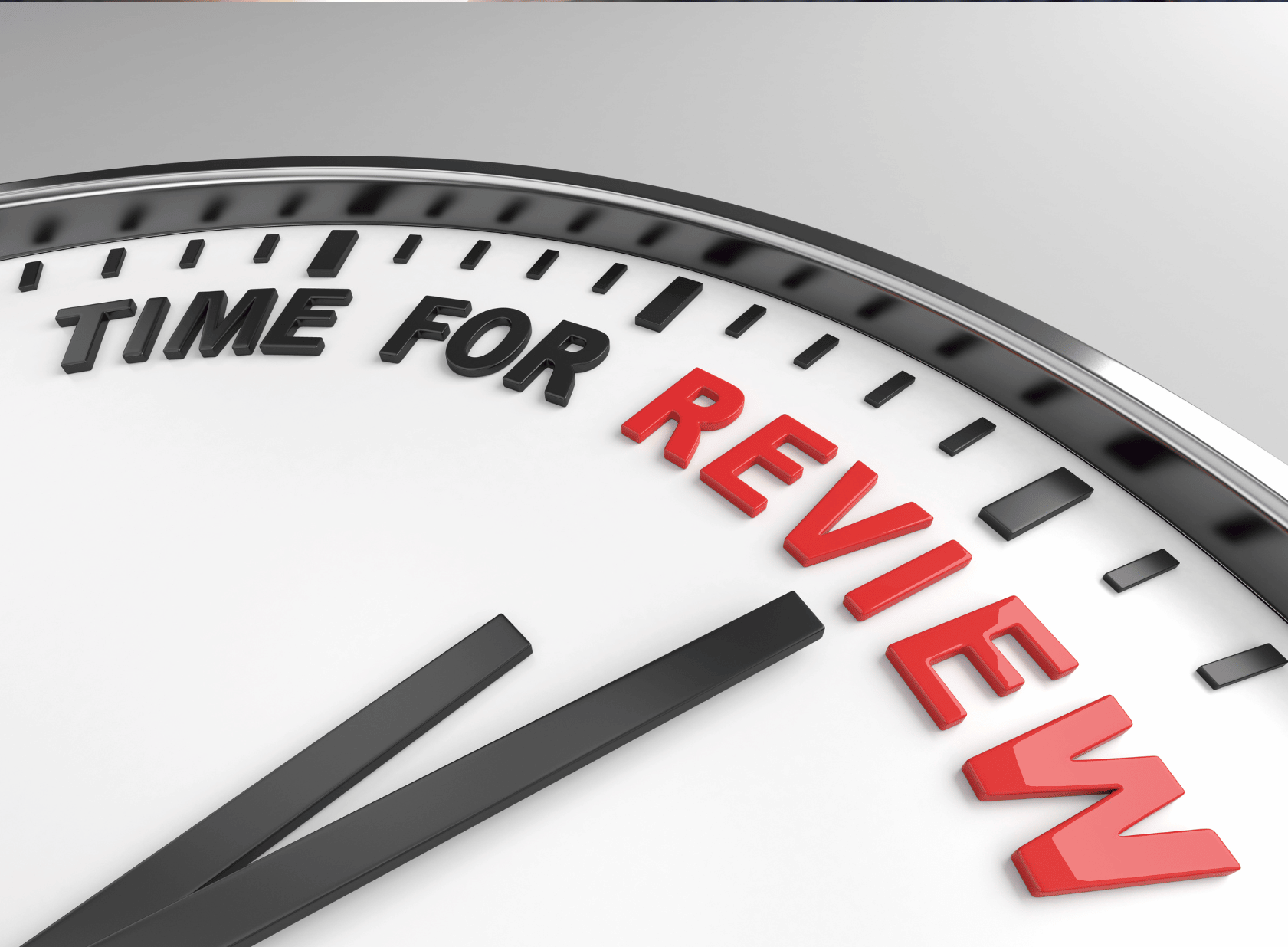
Conclusion
Workplace risk assessments are a fundamental part of your health and safety management, but their requirements can be blurry, so completing them correctly is vital to ensure the safety of your work premises. By ensuring your assessment includes these five key elements, you will create a strong foundation for a safer and more compliant workplace. Whilst the inclusion of staff into your practices will improve your workplace’s safety culture, ultimately creating a much safer working environment for everyone.