The working environment is constantly evolving, making it challenging to keep on top of health and safety. But with reports showing that almost 4 million working days are lost because of injuries every year in the UK, the presence of these common workplace hazards are clear.
Although every workplace has its own unique set of hazards, here are the most common workplace hazards that are likely lurking in your environment.
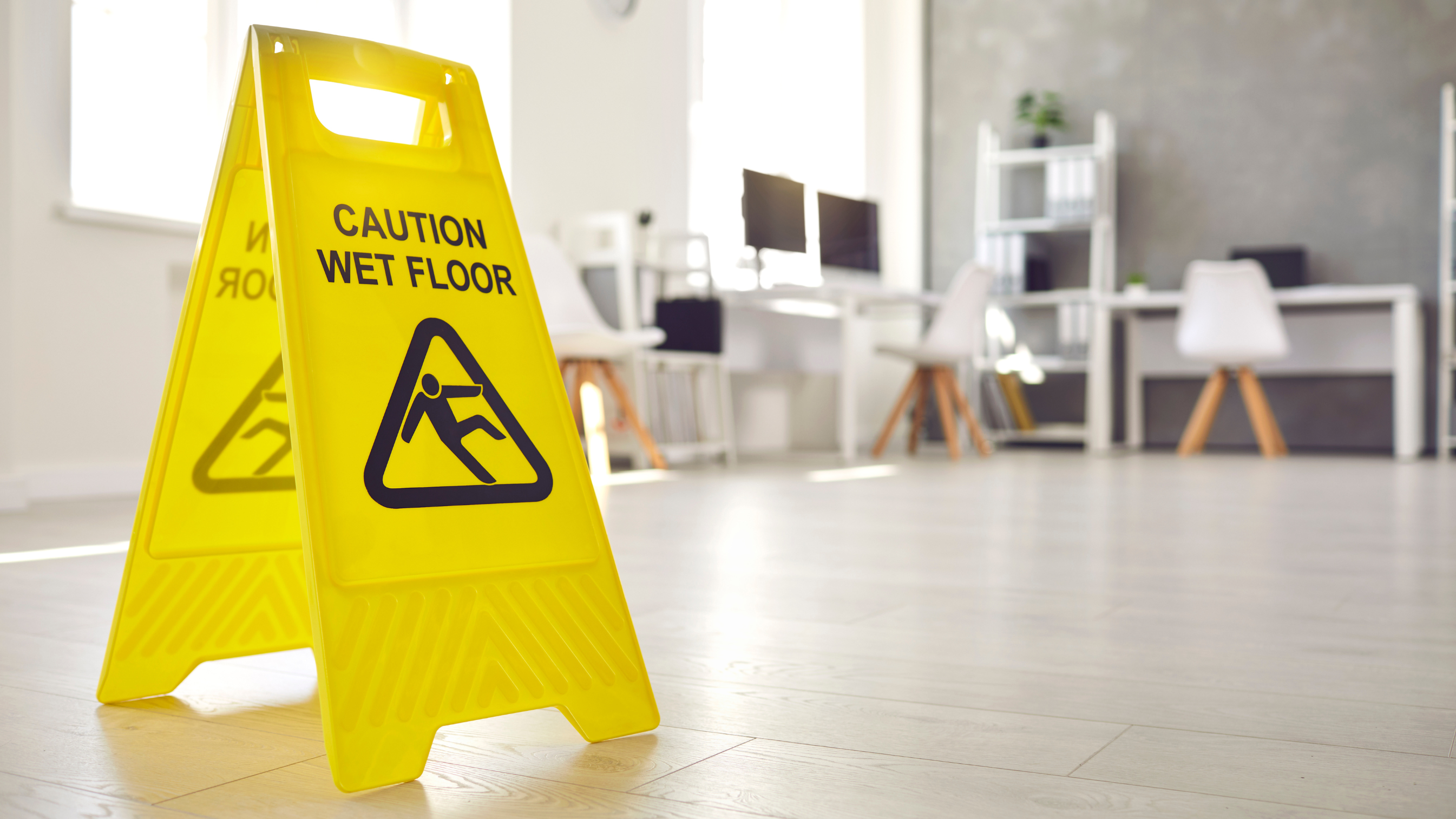
Slips, Trips and Falls
Accounting for almost a third (32%) of all injuries in 2023, slips, trips and falls are the most common cause of workplace injury in the UK, despite being one of the simpler hazards to spot and prevent.
One of the key preventative measures is ensuring good visibility. You should make sure that everyone can clearly see their path ahead, allowing them to double-check for any hazards eg. wet surfaces, objects in the way, uneven ground or steps. Areas should also be well-lit with walkways kept clear and dry, therefore ensuring that the path ahead can be seen.
It is also important to highlight any ‘problem areas’ to alert others to be more attentive. Some common methods to highlight these areas are:
- Signs – ‘Wet floor’ signs or ‘Caution when wet’ signs are some of the most widely used options.
- Highlighting steps – often bright grip tape is placed on ledges to highlight the elevation change to prevent trips.
- Slip-resistant flooring – Commonly placed near entrances to stop wet walkways from becoming a hazard.
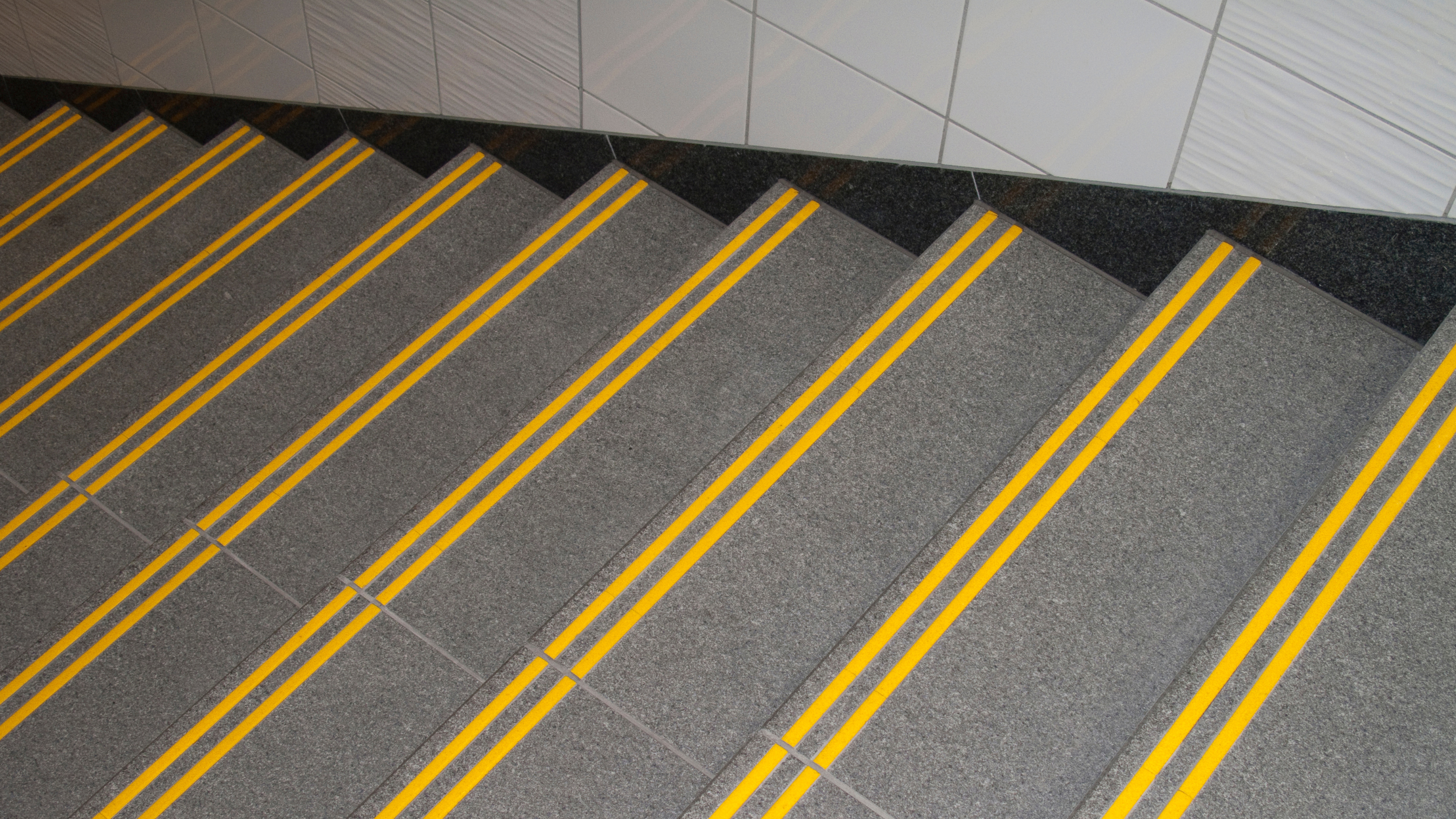
Fire Hazards
Fires remain a persistent and common hazard to businesses across the country, with a reported 22,000 workplace fires every year. To combat this, regular employee training is a necessity, and this can be done as a group session or online via a fire safety training course. Afterwards, taking this training periodically will refresh your employees’ knowledge.
It is also necessary to ensure that countermeasures are accounted for in case of a fire breaking out. This means checking your fire alarms and fire extinguishers regularly for damage, ensuring they are unobstructed and functional. Additionally, an evacuation plan should be in place, ensuring that everybody has a safe route out of the building – with any assistance necessary if needed.
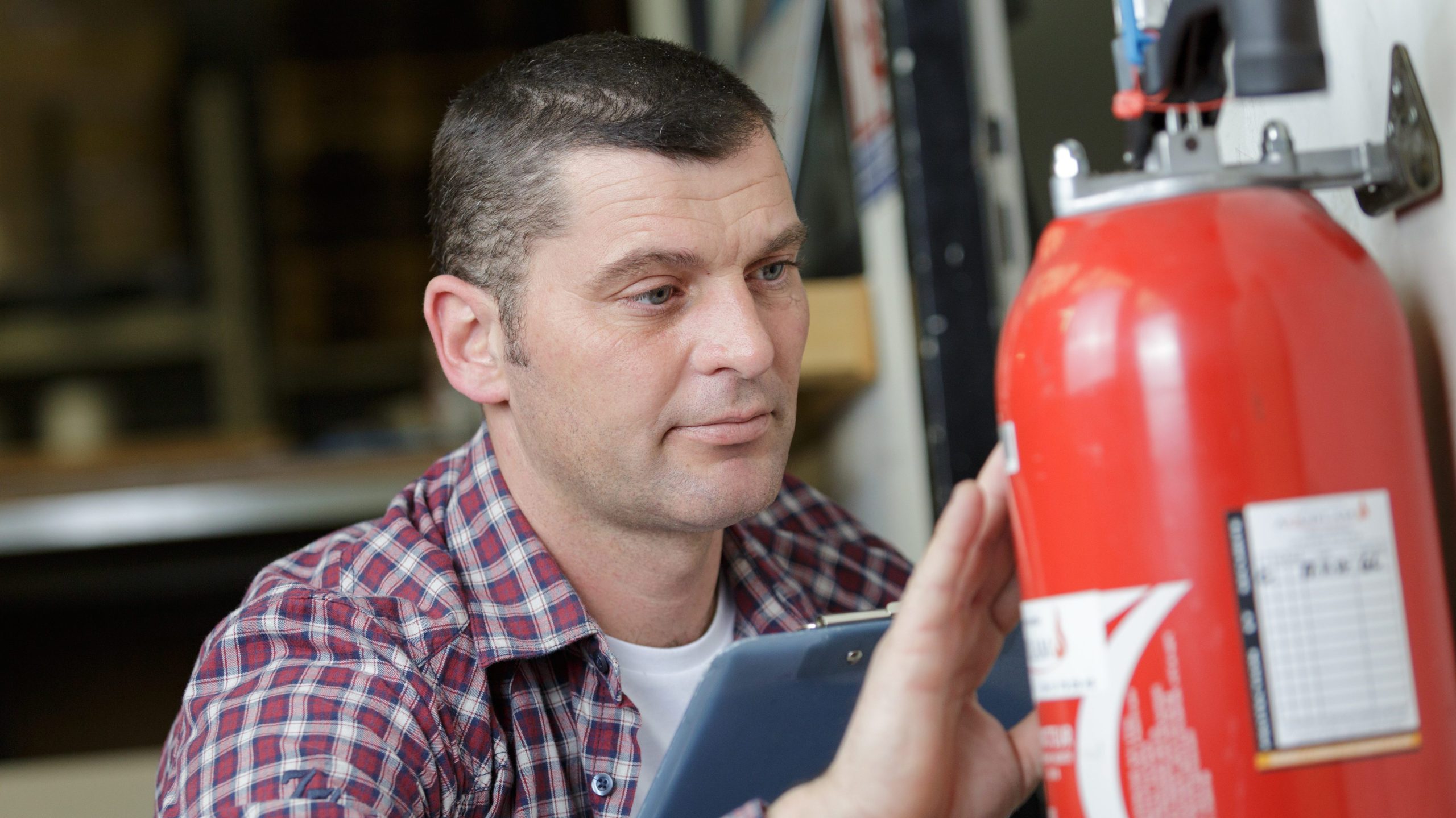
Electrical Hazards
Often forgotten, electrical hazards can pose a huge risk to your workplace safety if not regularly maintained. Shorting out circuits could potentially cause safety systems to fail, thereby increasing the risk of fires.
Simple yet regular checks are often the best way to keep on top of electrical risks, with formal maintenance and inspections carried out by a professional when necessary. Some key areas to check regularly are:
- Cables – are they all intact and insulated correctly, with no signs of damage?
- Outlets – are they in good condition and properly grounded?
- Overloading – are the outlets overloaded?
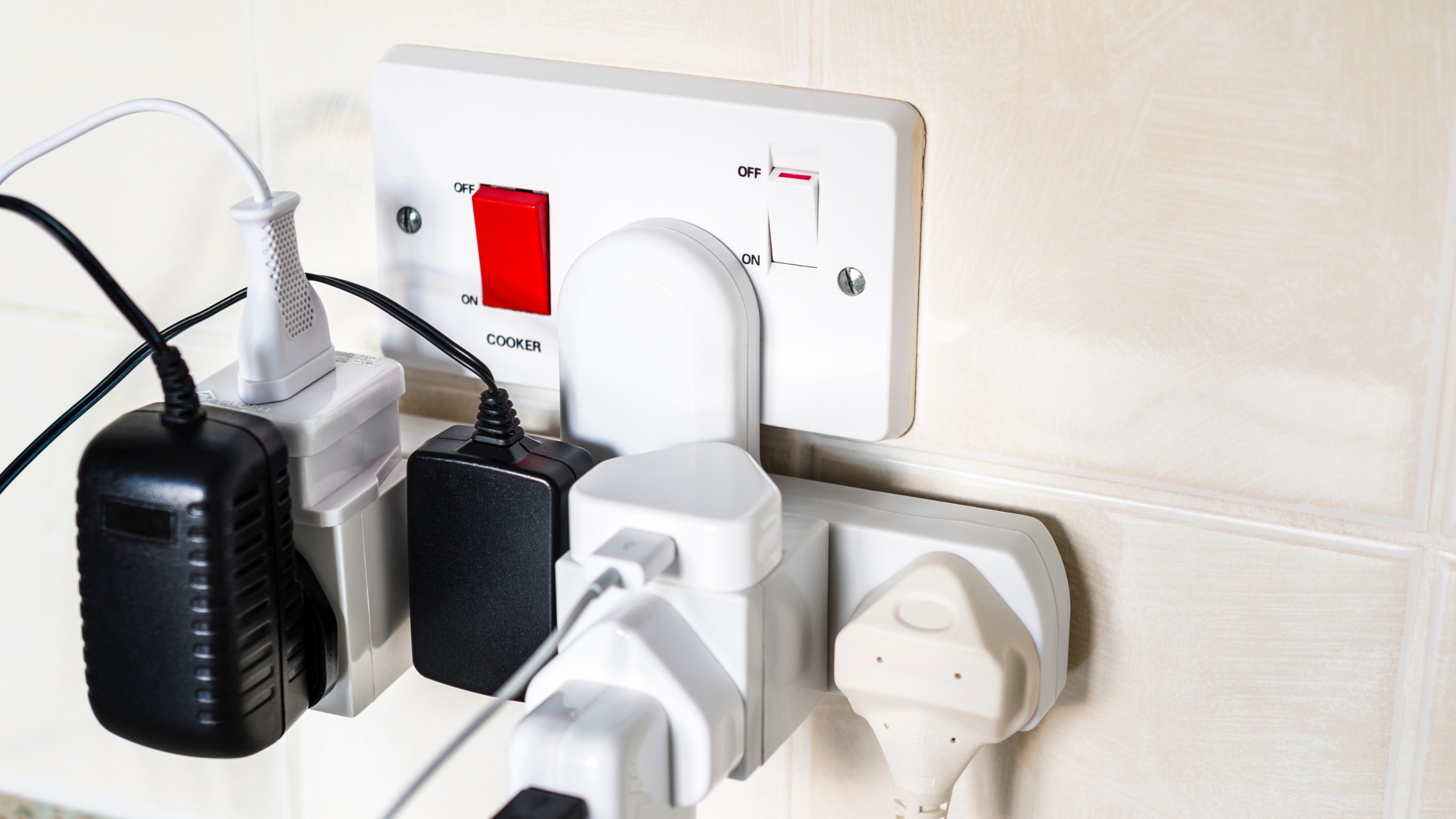
Ergonomic Hazards
Ergonomics often get disregarded when it comes to health and safety, but with almost half a million workers suffering from work-related musculoskeletal disorders every year in the UK, their importance is clear. Despite this high prevalence, it is one of the easier risks to eliminate.
Increasing awareness is the most common method to mitigate the hazards in the workplace, as employees can take more responsibility of their own workspace and adjust it accordingly. The best way to raise awareness among your staff is through training. A short eLearning course can effectively cover everything they need to know, and also gives you a record of when that was last completed.
Following on from the training, staff will then need to alter their workspaces to suit. This will involve adjusting everything from screen height for office workers to introducing equipment for heavy lifting for the more active sectors. Accommodating these changes will eliminate the ergonomic hazards, helping you prevent any injuries occurring because of poor ergonomics.
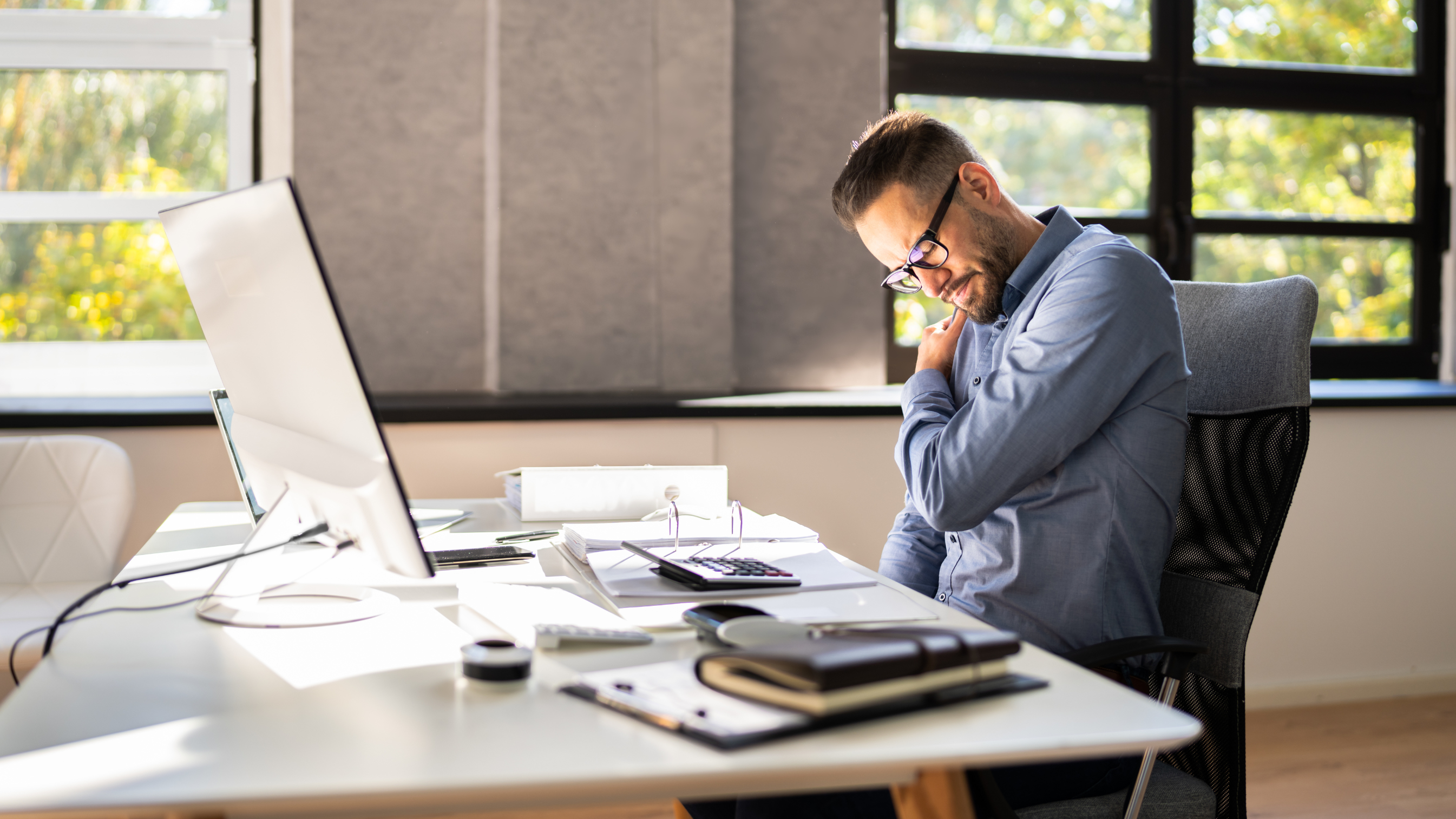
By identifying and eliminating these common workplace hazards, it can massively benefit both your business and your employees. This will help you to create a much safer and more efficient working environment, which will boost not only your business’s productivity but also its reputation. These implementations can all take place whilst also improving your staff’s morale and well-being by taking the ‘edge’ off your working environment; making it feel safer, whilst reducing staff injury and ill-health.
Sources:
HSE (2023) ‘Health and Safety at work statistics’. Available at: https://www.hse.gov.uk/statistics/overview.htm (Accessed: 27/06/2024)
Dorset Fire Protection (2023) ‘Common Causes of Workplace Fires’. Available at: https://dorsetfireprotection.co.uk/common-causes-workplace-fires/ (Accessed: 27/06/2024)